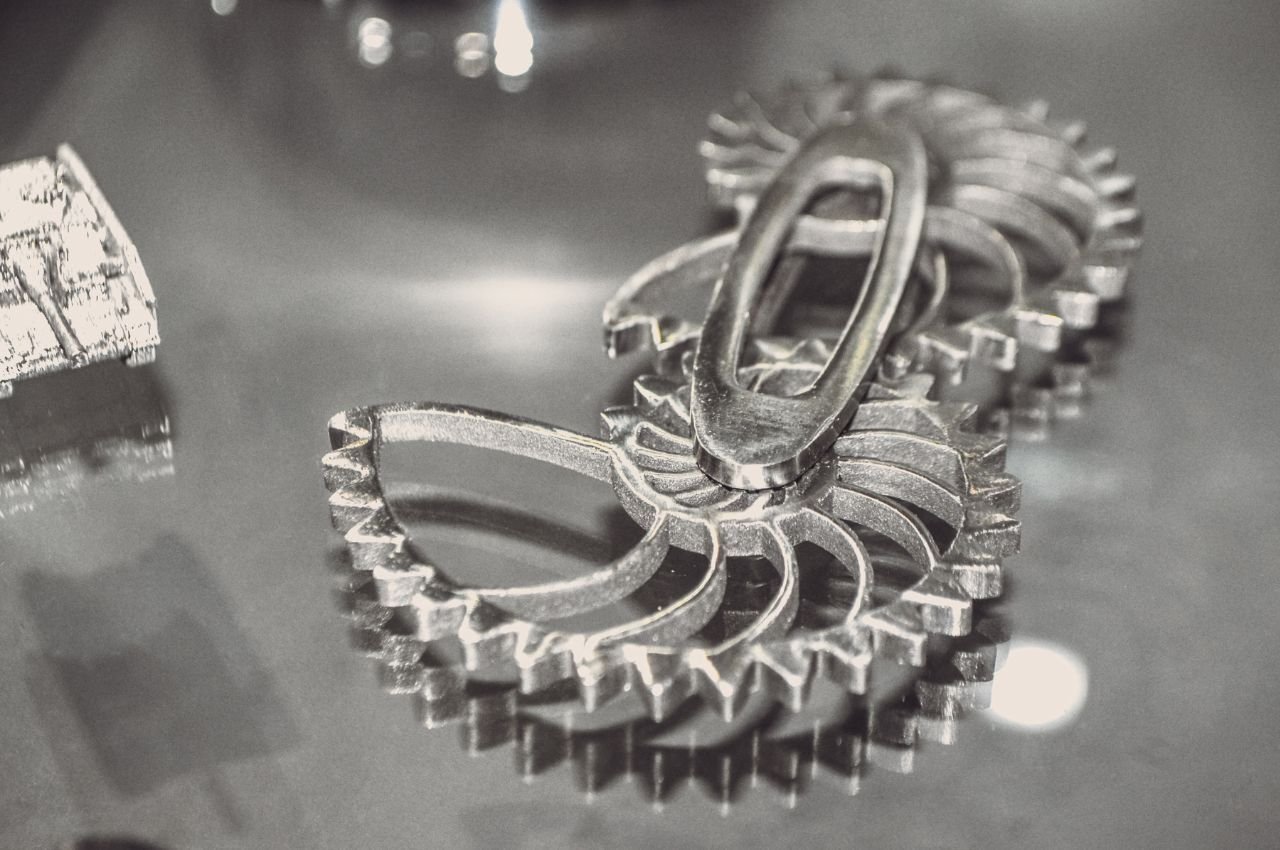
Welcome to the World of DMLS 3D Printing: Precision Metal Fabrication
Welcome to Ripley Dynamics, where we are proud to introduce you to the world of Direct Metal Laser Sintering (DMLS) 3D printing – the forefront of precision metal fabrication. DMLS is a cutting-edge technology that offers unparalleled precision in metal 3D printing, revolutionizing how industries approach manufacturing. This process involves using a laser to sinter powdered metal, layer by layer, to create highly detailed and complex metal components.
DMLS technology is ideal for producing parts that are difficult or impossible to manufacture through traditional methods. This includes items with intricate internal structures, complex geometries, and parts that require extreme precision. DMLS is not only revolutionary in terms of the complexity and precision it offers but also in its ability to significantly reduce production time and waste, making it a sustainable and efficient manufacturing solution.
At Ripley Dynamics, we harness the power of DMLS to offer innovative solutions across various industries, including aerospace, automotive, medical, and more. We are committed to pushing the boundaries of what's possible in metal fabrication, offering our clients in Australia the highest quality in metal 3D printing services..
Understanding DMLS
Direct Metal Laser Sintering (DMLS) is a sophisticated 3D printing technology that has transformed the realm of additive manufacturing, especially in working with metals. At its core, DMLS uses a high-powered laser to fuse metal powders together, layer by layer, to build parts directly from a digital model. This process allows for the creation of parts with complex geometries and fine internal structures that would be challenging or impossible to produce with conventional manufacturing techniques.
One of the key strengths of DMLS is its material versatility. It can work with a variety of metals, including stainless steel, titanium, aluminum, and cobalt chrome, making it suitable for numerous industrial applications. Another benefit is the high density and mechanical strength of the printed parts, comparable to those manufactured through traditional methods.
At Ripley Dynamics, our deep understanding of DMLS technology enables us to fully utilize its potential, providing advanced solutions that meet the specific needs of our clients. Whether for prototyping or end-use production, DMLS stands as a highly efficient, precise, and versatile manufacturing option.
Our Expert DMLS 3D Printing Service: Tailored Solutions for Your Needs
Ripley Dynamics specializes in providing expert Direct Metal Laser Sintering (DMLS) 3D printing services, delivering tailored solutions that meet the unique requirements of our clients. We understand that each project has its specific challenges and demands, and our team is equipped with the expertise to offer customized solutions.
Our process begins with a detailed consultation to understand your project’s objectives, material requirements, and design complexities. Leveraging the capabilities of DMLS, we can produce components with intricate geometries, internal channels, and complex details with a high degree of accuracy. We work with a range of metals, enabling us to create parts for diverse applications, from aerospace and automotive components to medical devices and custom tools.
At Ripley Dynamics, we pride ourselves on our meticulous approach to quality and precision. We ensure that every part we produce not only meets but exceeds industry standards, delivering exceptional performance and reliability. Our commitment to tailored solutions and quality makes us a preferred partner for DMLS 3D printing services in Australia.
Exploring the Capabilities of DMLS Machines and Metal Printers
At Ripley Dynamics, we harness the advanced capabilities of Direct Metal Laser Sintering (DMLS) machines and metal printers to offer superior additive manufacturing services. DMLS machines operate at the pinnacle of precision, using high-powered lasers to fuse metal powder into solid parts. They can produce parts with intricate details and complex geometries that traditional metalworking techniques cannot achieve.
Our DMLS printers are equipped to handle various metal powders, including stainless steel, titanium, and aluminum alloys, each offering unique properties for specific applications. These machines excel in creating lightweight, yet strong structures, and are capable of producing parts with internal features and channels, which are integral to applications like aerospace engineering and medical device manufacturing.
The precision of DMLS printers is unmatched, capable of producing parts with extremely tight tolerances and excellent surface finishes. This makes them ideal for creating highly detailed prototypes, as well as functional production parts that require exact specifications. With these advanced machines, Ripley Dynamics is pushing the boundaries of what's possible in metal fabrication and additive manufacturing.
Advantages of DMLS in Additive Manufacturing
Direct Metal Laser Sintering (DMLS) offers a host of advantages in the field of additive manufacturing, making it a preferred choice for a wide range of applications. Ripley Dynamics leverages these benefits to provide cutting-edge solutions to our clients. One of the primary advantages of DMLS is its ability to produce highly complex geometries and intricate details that are difficult or impossible to achieve with traditional manufacturing methods. This opens up new possibilities for design innovation and complexity.
Another significant advantage is the strength and durability of the parts produced. DMLS can create parts that are dense and structurally sound, suitable for critical applications in industries like aerospace, automotive, and medical devices. Additionally, DMLS offers a high degree of material efficiency, as it uses only the necessary material to build a part, significantly reducing waste.
DMLS also facilitates rapid prototyping, allowing for the quick creation and iteration of designs. This accelerates the development process, enabling faster product launches and the ability to respond swiftly to market changes. With these advantages, DMLS stands as a transformative technology in additive manufacturing, and Ripley Dynamics is proud to be at its forefront in Australia.
Custom Metal Prototyping with High-Quality DMLS Solutions
Custom metal prototyping is a vital component in product development, and Ripley Dynamics offers high-quality Direct Metal Laser Sintering (DMLS) solutions to meet this need. DMLS is particularly advantageous for prototyping, allowing designers and engineers to rapidly transform their ideas into tangible, high-fidelity metal parts. This technology facilitates the creation of prototypes that closely resemble the final product in terms of material properties and dimensional accuracy, enabling effective testing and validation processes.
Our DMLS solutions are ideal for producing complex prototypes that would be challenging to fabricate using traditional manufacturing methods. This includes components with intricate internal structures, complex geometries, or those that require a high degree of customization. With DMLS, changes to the design can be quickly implemented without the need for costly tooling adjustments, significantly accelerating the prototyping phase.
Ripley Dynamics ensures that each prototype is produced with the utmost precision and quality, adhering to strict industry standards. Our expert team works closely with clients to understand their specific requirements and deliver prototypes that aid in efficient product development and innovation
The Versatility of Metal 3D Printing Materials in DMLS
The versatility of metal 3D printing materials available in Direct Metal Laser Sintering (DMLS) significantly expands the potential applications of this technology. Ripley Dynamics offers a diverse range of metal powders for DMLS, each with unique properties to suit various application requirements. Common materials include stainless steel, known for its strength and corrosion resistance, making it suitable for a wide range of industrial applications.
Titanium is another popular choice, especially in aerospace and medical applications, due to its lightweight, strength, and biocompatibility. Aluminum alloys are preferred for applications where weight is a critical factor, offering a good balance of strength and lightness. In addition, more specialized materials like nickel alloys, cobalt chrome, and precious metals are available for specific high-performance applications.
Each material brings different properties to the table, such as thermal resistance, ductility, and hardness, which can be leveraged to optimize the performance of the final part. Understanding these materials' properties is crucial in choosing the right one for a specific application, and Ripley Dynamics’ expertise ensures that our clients make informed decisions to achieve the best results.
Finishing Techniques: Enhancing Your DMLS 3D Printed Parts
Once a part is produced using Direct Metal Laser Sintering (DMLS), various finishing techniques can be applied to enhance its physical appearance and functional properties. Ripley Dynamics provides a range of finishing options for DMLS 3D printed parts, ensuring they meet the desired aesthetic and performance criteria. One common finishing technique is sandblasting, which smooths and evens out the surface, providing a uniform matte finish.
For parts requiring a more polished appearance, mechanical polishing or chemical processes can be used to achieve a high-gloss finish. This is particularly important in consumer products and high-visibility components. If additional surface hardness or wear resistance is needed, heat treatment and anodizing can be applied.
For parts that will be used in functional applications, coatings can be applied to enhance characteristics like corrosion resistance or thermal conductivity. Ripley Dynamics works closely with clients to understand the intended use of their DMLS parts and advises on the best finishing techniques to optimize the parts’ appearance and functionality.
Designing for DMLS: Best Practices and Considerations
Designing for Direct Metal Laser Sintering (DMLS) requires a specific approach to fully utilize the capabilities of this technology. At Ripley Dynamics, we guide our clients through the best practices and considerations essential for DMLS. One key aspect is designing for the additive manufacturing process, which includes considering the orientation of the part during printing and the support structures required.
Complex geometries, internal channels, and fine details can be achieved with DMLS, but it’s important to maintain realistic wall thicknesses and avoid overly intricate designs that might compromise structural integrity. Designers should also factor in the inherent characteristics of the metal powder being used and how it will affect the part’s performance.
We also emphasize the importance of post-processing in the design phase. Understanding the limitations and possibilities of various finishing techniques can influence the design choices made early in the process. By considering these factors, designers can create parts that not only capitalize on the strengths of DMLS but also are cost-effective and functionally efficient.
Innovative Applications: Exploring the Best Uses for DMLS Technology
Direct Metal Laser Sintering (DMLS) technology has a broad spectrum of innovative applications, pushing the boundaries of what’s possible in various industries. At Ripley Dynamics, we explore and implement DMLS for applications where its unique capabilities can be fully leveraged. In the aerospace industry, DMLS is used for manufacturing lightweight, yet robust components, contributing to more efficient aircraft designs.
The medical sector benefits significantly from DMLS in creating custom implants and prosthetics, tailored to individual patient anatomy. This technology is also revolutionizing the dental industry by enabling the production of high-precision dental implants and crowns. In automotive manufacturing, DMLS is used for producing complex, lightweight components that enhance vehicle performance and fuel efficiency.
The tooling industry is another area where DMLS excels, allowing for the creation of molds with complex cooling channels that improve production efficiency. These applications illustrate the transformative potential of DMLS technology in various fields, something that Ripley Dynamics is committed to advancing in Australia’s additive manufacturing landscape.